eat-cured plastics called thermosets can’t be beat for their long lives. But these resilient polymers, used to make coatings, car parts, and dishes, have a flaw: they can’t be reshaped or recycled. Now, a new plastic features the toughness of thermosets in a more sustainable package. Unlike its predecessors, it can be melted and reformed […]
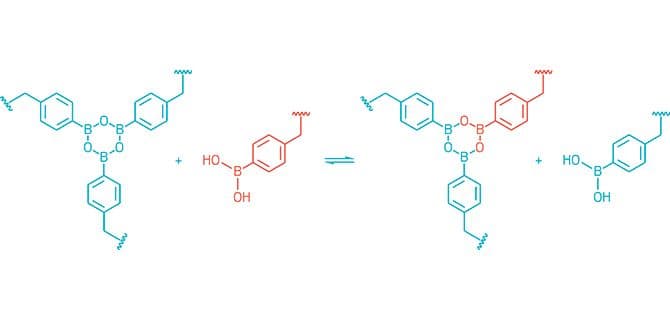
eat-cured plastics called thermosets can’t be beat for their long lives. But these resilient polymers, used to make coatings, car parts, and dishes, have a flaw: they can’t be reshaped or recycled. Now, a new plastic features the toughness of thermosets in a more sustainable package. Unlike its predecessors, it can be melted and reformed into a new object that is just as strong as the original, or broken down into its starting material, which can be reused to make new polymers.
Thermoset plastics, which include materials like epoxy resin and melamine, are produced by heating liquid raw materials or reacting them with a catalyst. They are hard, strong, and resist chemical corrosion and high temperatures. But those impressive mechanical properties mean that once a melamine plate cracks, it typically ends up in a landfill.
In recent years, researchers have developed a more malleable class of thermoset called a vitrimer that can be shaped like glass when heated, but keeps its toughness when cool. These are based on cross-links that break and reform at elevated temperatures. But so far, it has been difficult to make a vitrimer with high mechanical strength that can be easily melted and remolded multiple times, and broken down into its raw materials to be recycled, says chemist Zhibin Guan at the University of California, Irvine.
Guan’s group examined boron-oxygen bonds because they are “thermodynamically very stable and strong bonds,” he says. From previous work, they knew that boron-oxygen bonds could be made flexible. In particular, he and his graduate student William Ogden turned to boroxine, a compound with a six-membered ring of alternating boron and oxygen atoms made by dehydrating boronic acid.
The researchers started with diboronic acid monomers. They made a solution of the monomers and a pyridine-based plasticizer, poured it into a dish, and heated it to 80°C for 12 hours. This dehydration produced a stiff, strong boroxine-based thermoset insoluble in organic solvents.
The material could be reshaped when the researchers applied pressure and heat, and even at room temperature if pressure was applied for a long enough time. Boroxine rings are fluid: They break and then reform in another part of the polymer network when they react with residual boronic acid groups. “It’s like a harder, more robust version of silly putty,” Guan says.
These properties also allowed the polymer to be reprocessed. The researchers repeatedly cut the sample into pieces and hot-pressed them in a mold to reform a new sample without any loss in mechanical properties.
But the last test demonstrated the full recyclability of the material: They dissolved the plastic in boiling water and cooled the solution to recover the starting monomer, a white powder of diboronic acid.
The plastic could be tailored for coatings, adhesives, fillers for composites, and for 3-D printing, Guan says. Plus, the chemical components are inexpensive and readily available, so large quantities should be easy to make.
This is a nice design strategy for malleable thermoset polymers, says Wei Zhang, a chemist at the University of Colorado, Boulder. The ability to degrade plastics to their constituent monomers would minimize chemical waste and provide a greener, more eco-friendly approach to plastics, he says. Practically, however, the researchers need to thoroughly study this new material’s resistance to moisture; This new material fully dissolves in boiling water, which could limit its applications.
Guan says that there are many ways to tune the properties of this initial proof-of-concept system. “By putting more hydrophobic components in the monomer unit, we should be able to make it much more stable toward water.”
This article is reproduced with permission from C&EN (© American Chemical Society). The article was first published on May 31, 2018.