By teaming tiny capsules of dye with an emerging medical imaging technology, researchers can reveal micrometers-thin cracks lurking inside plastics and composites. The advance could lead to an early-warning system for aerospace parts, medical implants, and oil pipeline coatings, identifying tiny fractures before they grow large enough to trigger failure. The technique allows the researchers […]
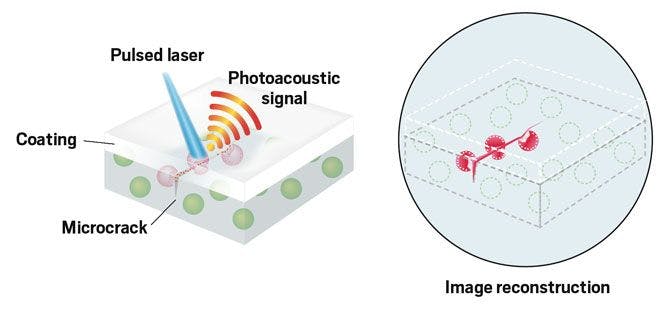
By teaming tiny capsules of dye with an emerging medical imaging technology, researchers can reveal micrometers-thin cracks lurking inside plastics and composites. The advance could lead to an early-warning system for aerospace parts, medical implants, and oil pipeline coatings, identifying tiny fractures before they grow large enough to trigger failure.
The technique allows the researchers to image micro-fractures that are 1 cm deep, and it should work even deeper, says Jefferson Chan, a chemist at the University of Illinois at Urbana-Champaign. While standard ultrasound imaging can detect advanced internal damage, Chan says, “we’re trying to diagnose early, when they’re still micro-cracks.”
Researchers have previously used damage-indicating plastics to reveal surface micro-cracks. These plastics typically contain tiny channels or beads that rupture when the plastic begins to crack, spilling chemicals that fluoresce or change color. But these visual cues cannot reveal deeper damage, because such cues would not travel through most materials.
Microcapsules (green) incorporated into an amine-containing epoxy resin rupture and release a pH-sensitive dye (red dots) when a crack forms. The released dye reacts with the amines in the resin, which allows it to absorb the pulsed laser light and emit a photoacoustic signal that is used to construct an image that reveals the crack.
Chan and his colleagues turned to photoacoustic imaging, a nascent medical imaging technology in which safe laser pulses are fired into tissue, making it quickly heat up and expand. As the tissue relaxes, it releases ultrasonic waves that are analyzed using the same process as regular ultrasound to produce high-resolution images.
To apply this technique to structural materials, the research team embedded microcapsules containing a pH-responsive, near-infrared dye in an amine-containing epoxy resin. The researchers monitored the resin by scanning it with laser light at a wavelength of 760 nm.
The dye within the capsules absorbs light at a near-IR wavelength of 680 nm, so the laser has no effect if the resin is unscathed. But when the material is damaged, the microcapsules break and release the dye, which reacts with the amine in the resin. This changes the dye’s pH and causes it to absorb light at 760 nm. Now, light pulses from the laser can excite the dye, heating it enough to generate a photoacoustic signal that is used to construct images.
To prove the system’s mettle, the team made 1- to 7.5-µm-wide scratches on resin samples, and then coated them with a 0.5-cm-thick layer of opaque gel. Photoacoustic images clearly showed all the cracks, even though they were invisible to the eye. The widest crack was clearly visible even under a 1-cm-thick gel layer. The method should work with any material as long as light can penetrate it, Chan says. It would not work for solid metal, for instance.
The visualization depth, meanwhile, is limited by his group’s laboratory equipment, which is meant for imaging small animals. State-of-the-art photoacoustic imagers can visualize cracks at high-resolution at depths of 8 to 10 cm, he says.
Christoph Weder, a polymer and materials chemist at the University of Fribourg says that the technique is exciting. It’s a clever, elegant way to “look inside” materials and detect micro-cracks, he says, and it should be fairly easy to apply it to other dyes and polymers. One concern, he says, is that current photoacoustic imaging methods might not be easy to use in a routine manner to monitor structures.
This could soon change. Photoacoustic imaging is a rapidly growing field, Chan says. “People are now developing handheld instrumentation that could expand the use of this technology.”
This article is reproduced with permission from C&EN (© American Chemical Society). The article was first published on April 20, 2018.