Epoxides are ubiquitous in the manufacture of consumer goods, including polyester clothing, antifreeze, and pharmaceuticals. Using current techniques, epoxide synthesis reactions produce high direct CO2 emissions and require hazardous reagents, high temperatures, and high pressures, meaning that the industrial process poses both safety and environmental risks. In a new study, researchers have shown that an […]
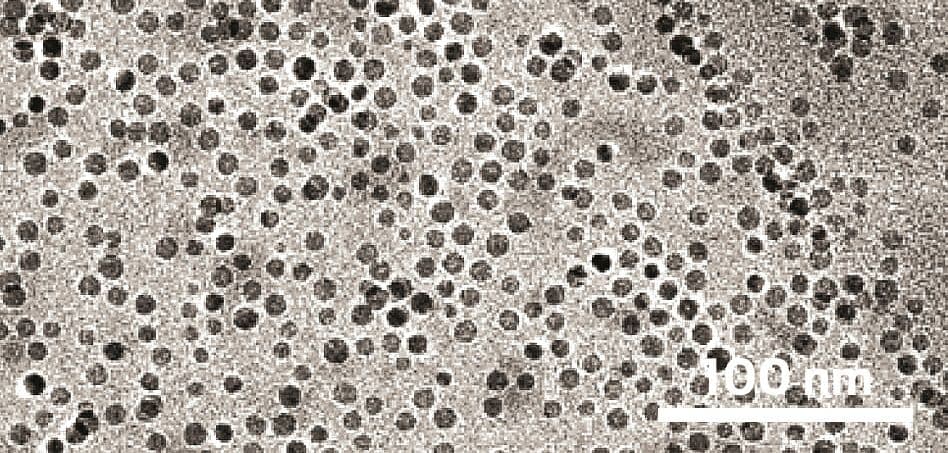
Epoxides are ubiquitous in the manufacture of consumer goods, including polyester clothing, antifreeze, and pharmaceuticals. Using current techniques, epoxide synthesis reactions produce high direct CO2 emissions and require hazardous reagents, high temperatures, and high pressures, meaning that the industrial process poses both safety and environmental risks. In a new study, researchers have shown that an electrochemical cell can make epoxides from olefins at room temperature and pressure. This reaction produces minimal waste products and no CO2 as part of the process chemistry.
The traditional process for producing ethylene oxide, for example, is to combine ethylene and oxygen at a temperature of 270–290 °C and a pressure of 1–3 MPa. But CO2 inevitably forms as a result of over-oxidation, which increases the process’s built-in CO2 footprint.
To reduce this footprint, Karthish Manthiram, a chemical engineer at MIT, and coworkers developed an electrochemical method that splits water to provide a source of oxygen for the epoxidation reaction. In a one-compartment electrochemical cell, they mixed various olefins and nanoparticles of manganese oxide (a known water-splitting catalyst) into a blend of acetonitrile and water. Putting 2.5 mA/cm2 of current across the cell and using cyclooctene as the olefin produced cyclooctene oxide and hydrogen, with 50% of the olefins converted after 4 h.
Since olefins and water don’t normally react at room temperature and pressure, it’s counterintuitive to think of reacting olefins in water, Manthiram says. “That’s the very special thing about an electrochemical approach.” Scientists usually split water to produce hydrogen and just vent off the oxygen, he says. Instead, this new method grabs the oxygen atom that comes from water and transfers it to an olefin. The hydrogen produced is a bonus: “you end up with a second valuable product” that can help make it easier for the process to be commercially viable, he says.
“From the environmental perspective, chemistry that produces such an important functional group from olefins and water for organic synthesis and only generates hydrogen along with the epoxide product seems, conceptually, very attractive,” says Bruce H. Lipshutz, an organic chemist at the University of California, Santa Barbara, who focuses on green chemistry. However, he says, several obvious issues would need to be addressed to move the chemistry forward for widespread use in the future.
One of the biggest is the use of acetonitrile as a solvent in the reaction, and that’s something Manthiram’s group is working on eliminating. Although generating acetonitrile waste can be tolerated in small-scale syntheses, such as those used to make pharmaceuticals, a purely aqueous electrolyte is going to be essential for this reaction to be scaled up to industrial levels, Manthiram says. But he’s still thrilled at their success so far. “I would characterize this as an early stage, fundamental discovery. It opens up a lot of possibilities.”
If Manthiram’s group can work through some of the issues with the system, “it could be spectacular,” Lipshutz says. “Why wouldn’t anyone want to get the oxygen from water?”